About Stanford GSB
- The Leadership
- Dean’s Updates
- School News & History
- Commencement
- Business, Government & Society
- Centers & Institutes
- Center for Entrepreneurial Studies
- Center for Social Innovation
- Stanford Seed

About the Experience
- Learning at Stanford GSB
- Experiential Learning
- Guest Speakers
- Entrepreneurship
- Social Innovation
- Communication
- Life at Stanford GSB
- Collaborative Environment
- Activities & Organizations
- Student Services
- Housing Options
- International Students
Full-Time Degree Programs
- Why Stanford MBA
- Academic Experience
- Financial Aid
- Why Stanford MSx
- Research Fellows Program
- See All Programs
Non-Degree & Certificate Programs
- Executive Education
- Stanford Executive Program
- Programs for Organizations
- The Difference
- Online Programs
- Stanford LEAD
- Seed Transformation Program
- Aspire Program
- Seed Spark Program
- Faculty Profiles
- Academic Areas
- Awards & Honors
- Conferences
Faculty Research
- Publications
- Working Papers
- Case Studies
Research Hub
- Research Labs & Initiatives
- Business Library
- Data, Analytics & Research Computing
- Behavioral Lab
Research Labs
- Cities, Housing & Society Lab
- Golub Capital Social Impact Lab
Research Initiatives
- Corporate Governance Research Initiative
- Corporations and Society Initiative
- Policy and Innovation Initiative
- Rapid Decarbonization Initiative
- Stanford Latino Entrepreneurship Initiative
- Value Chain Innovation Initiative
- Venture Capital Initiative
- Career & Success
- Climate & Sustainability
- Corporate Governance
- Culture & Society
- Finance & Investing
- Government & Politics
- Leadership & Management
- Markets and Trade
- Operations & Logistics
- Opportunity & Access
- Technology & AI
- Opinion & Analysis
- Email Newsletter
Welcome, Alumni
- Communities
- Digital Communities & Tools
- Regional Chapters
- Women’s Programs
- Identity Chapters
- Find Your Reunion
- Career Resources
- Job Search Resources
- Career & Life Transitions
- Programs & Webinars
- Career Video Library
- Alumni Education
- Research Resources
- Volunteering
- Alumni News
- Class Notes
- Alumni Voices
- Contact Alumni Relations
- Upcoming Events
Admission Events & Information Sessions
- MBA Program
- MSx Program
- PhD Program
- Alumni Events
- All Other Events
- Operations, Information & Technology
- Organizational Behavior
- Political Economy
- Classical Liberalism
- The Eddie Lunch
- Accounting Summer Camp
- California Econometrics Conference
- California Quantitative Marketing PhD Conference
- California School Conference
- China India Insights Conference
- Homo economicus, Evolving
- Political Economics (2023–24)
- Scaling Geologic Storage of CO2 (2023–24)
- A Resilient Pacific: Building Connections, Envisioning Solutions
- Adaptation and Innovation
- Changing Climate
- Civil Society
- Climate Impact Summit
- Climate Science
- Corporate Carbon Disclosures
- Earth’s Seafloor
- Environmental Justice
- Operations and Information Technology
- Organizations
- Sustainability Reporting and Control
- Taking the Pulse of the Planet
- Urban Infrastructure
- Watershed Restoration
- Junior Faculty Workshop on Financial Regulation and Banking
- Ken Singleton Celebration
- Marketing Camp
- Quantitative Marketing PhD Alumni Conference
- Presentations
- Theory and Inference in Accounting Research
- Stanford Closer Look Series
- Quick Guides
- Core Concepts
- Journal Articles
- Glossary of Terms
- Faculty & Staff
- Subscribe to Corporate Governance Emails
- Researchers & Students
- Research Approach
- Charitable Giving
- Financial Health
- Government Services
- Workers & Careers
- Short Course
- Adaptive & Iterative Experimentation
- Incentive Design
- Social Sciences & Behavioral Nudges
- Bandit Experiment Application
- Conferences & Events
- Get Involved
- Reading Materials
- Teaching & Curriculum
- Energy Entrepreneurship
- Faculty & Affiliates
- SOLE Report
- Responsible Supply Chains
- Current Study Usage
- Pre-Registration Information
- Participate in a Study
Unsafe For Children: Mattel’s Toy Recalls and Supply Chain Management
In August and September 2007, Mattel made a series of product recalls, totaling more than 20 million toys. The recalls were for excessive lead and for magnets that could become loose. All of the recalled toys had been made in China. The Mattel recalls followed on the heels of a number of high profile safety problems with Chinese imports, including contaminated pet food and toothpaste, defective tires, and lead-painted toys. The recalls sparked intense criticism of Mattel and its Chinese supply chain, despite the fact that more than 85 percent of the recalled toys were due to design problems (magnets), not the result of improper manufacturing (use of lead paint). The case provides a basis for discussion of outsourcing and supply chain management. The basic toy manufacturing process is fairly simple, providing a forum for discussing these issues without the complication of advanced manufacturing technology or an involved supply chain. In this case, supply chain defects, such as the use of lead paint by vendors, can have severe consequences. The supply chain must be designed to prevent these defects. The case enables discussion of why companies outsource, managing a supply chain, and the appropriate use of inspection and testing. It also provides the opportunity to examine response to a crisis situation, and the relationship between a company and government.

- See the Current DEI Report
- Supporting Data
- Research & Insights
- Share Your Thoughts
- Search Fund Primer
- Affiliated Faculty
- Faculty Advisors
- Louis W. Foster Resource Center
- Defining Social Innovation
- Impact Compass
- Global Health Innovation Insights
- Faculty Affiliates
- Student Awards & Certificates
- Changemakers
- Dean Jonathan Levin
- Dean Garth Saloner
- Dean Robert Joss
- Dean Michael Spence
- Dean Robert Jaedicke
- Dean Rene McPherson
- Dean Arjay Miller
- Dean Ernest Arbuckle
- Dean Jacob Hugh Jackson
- Dean Willard Hotchkiss
- Faculty in Memoriam
- Stanford GSB Firsts
- Annual Alumni Dinner
- Class of 2024 Candidates
- Certificate & Award Recipients
- Dean’s Remarks
- Keynote Address
- Teaching Approach
- Analysis and Measurement of Impact
- The Corporate Entrepreneur: Startup in a Grown-Up Enterprise
- Data-Driven Impact
- Designing Experiments for Impact
- Digital Marketing
- The Founder’s Right Hand
- Marketing for Measurable Change
- Product Management
- Public Policy Lab: Financial Challenges Facing US Cities
- Public Policy Lab: Homelessness in California
- Lab Features
- Curricular Integration
- View From The Top
- Formation of New Ventures
- Managing Growing Enterprises
- Startup Garage
- Explore Beyond the Classroom
- Stanford Venture Studio
- Summer Program
- Workshops & Events
- The Five Lenses of Entrepreneurship
- Leadership Labs
- Executive Challenge
- Arbuckle Leadership Fellows Program
- Selection Process
- Training Schedule
- Time Commitment
- Learning Expectations
- Post-Training Opportunities
- Who Should Apply
- Introductory T-Groups
- Leadership for Society Program
- Certificate
- 2024 Awardees
- 2023 Awardees
- 2022 Awardees
- 2021 Awardees
- 2020 Awardees
- 2019 Awardees
- 2018 Awardees
- Social Management Immersion Fund
- Stanford Impact Founder Fellowships
- Stanford Impact Leader Prizes
- Social Entrepreneurship
- Stanford GSB Impact Fund
- Economic Development
- Energy & Environment
- Stanford GSB Residences
- Environmental Leadership
- Stanford GSB Artwork
- A Closer Look
- California & the Bay Area
- Voices of Stanford GSB
- Business & Beneficial Technology
- Business & Sustainability
- Business & Free Markets
- Business, Government, and Society Forum
- Second Year
- Global Experiences
- JD/MBA Joint Degree
- MA Education/MBA Joint Degree
- MD/MBA Dual Degree
- MPP/MBA Joint Degree
- MS Computer Science/MBA Joint Degree
- MS Electrical Engineering/MBA Joint Degree
- MS Environment and Resources (E-IPER)/MBA Joint Degree
- Academic Calendar
- Clubs & Activities
- LGBTQ+ Students
- Military Veterans
- Minorities & People of Color
- Partners & Families
- Students with Disabilities
- Student Support
- Residential Life
- Student Voices
- MBA Alumni Voices
- A Week in the Life
- Career Support
- Employment Outcomes
- Cost of Attendance
- Knight-Hennessy Scholars Program
- Yellow Ribbon Program
- BOLD Fellows Fund
- Application Process
- Loan Forgiveness
- Contact the Financial Aid Office
- Evaluation Criteria
- GMAT & GRE
- English Language Proficiency
- Personal Information, Activities & Awards
- Professional Experience
- Letters of Recommendation
- Optional Short Answer Questions
- Application Fee
- Reapplication
- Deferred Enrollment
- Joint & Dual Degrees
- Entering Class Profile
- Event Schedule
- Ambassadors
- New & Noteworthy
- Ask a Question
- See Why Stanford MSx
- Is MSx Right for You?
- MSx Stories
- Leadership Development
- How You Will Learn
- Admission Events
- Personal Information
- GMAT, GRE & EA
- English Proficiency Tests
- Career Change
- Career Advancement
- Career Support and Resources
- Daycare, Schools & Camps
- U.S. Citizens and Permanent Residents
- Requirements
- Requirements: Behavioral
- Requirements: Quantitative
- Requirements: Macro
- Requirements: Micro
- Annual Evaluations
- Field Examination
- Research Activities
- Research Papers
- Dissertation
- Oral Examination
- Current Students
- Education & CV
- International Applicants
- Statement of Purpose
- Reapplicants
- Application Fee Waiver
- Deadline & Decisions
- Job Market Candidates
- Academic Placements
- Stay in Touch
- Faculty Mentors
- Current Fellows
- Standard Track
- Fellowship & Benefits
- Group Enrollment
- Program Formats
- Developing a Program
- Diversity & Inclusion
- Strategic Transformation
- Program Experience
- Contact Client Services
- Campus Experience
- Live Online Experience
- Silicon Valley & Bay Area
- Digital Credentials
- Faculty Spotlights
- Participant Spotlights
- Eligibility
- International Participants
- Stanford Ignite
- Frequently Asked Questions
- Founding Donors
- Program Contacts
- Location Information
- Participant Profile
- Network Membership
- Program Impact
- Collaborators
- Entrepreneur Profiles
- Company Spotlights
- Seed Transformation Network
- Responsibilities
- Current Coaches
- How to Apply
- Meet the Consultants
- Meet the Interns
- Intern Profiles
- Collaborate
- Research Library
- News & Insights
- Databases & Datasets
- Research Guides
- Consultations
- Research Workshops
- Career Research
- Research Data Services
- Course Reserves
- Course Research Guides
- Material Loan Periods
- Fines & Other Charges
- Document Delivery
- Interlibrary Loan
- Equipment Checkout
- Print & Scan
- MBA & MSx Students
- PhD Students
- Other Stanford Students
- Faculty Assistants
- Research Assistants
- Stanford GSB Alumni
- Telling Our Story
- Staff Directory
- Site Registration
- Alumni Directory
- Alumni Email
- Privacy Settings & My Profile
- Success Stories
- The Story of Circles
- Support Women’s Circles
- Stanford Women on Boards Initiative
- Alumnae Spotlights
- Insights & Research
- Industry & Professional
- Entrepreneurial Commitment Group
- Recent Alumni
- Half-Century Club
- Fall Reunions
- Spring Reunions
- MBA 25th Reunion
- Half-Century Club Reunion
- Faculty Lectures
- Ernest C. Arbuckle Award
- Alison Elliott Exceptional Achievement Award
- ENCORE Award
- Excellence in Leadership Award
- John W. Gardner Volunteer Leadership Award
- Robert K. Jaedicke Faculty Award
- Jack McDonald Military Service Appreciation Award
- Jerry I. Porras Latino Leadership Award
- Tapestry Award
- Student & Alumni Events
- Executive Recruiters
- Interviewing
- Land the Perfect Job with LinkedIn
- Negotiating
- Elevator Pitch
- Email Best Practices
- Resumes & Cover Letters
- Self-Assessment
- Whitney Birdwell Ball
- Margaret Brooks
- Bryn Panee Burkhart
- Margaret Chan
- Ricki Frankel
- Peter Gandolfo
- Cindy W. Greig
- Natalie Guillen
- Carly Janson
- Sloan Klein
- Sherri Appel Lassila
- Stuart Meyer
- Tanisha Parrish
- Virginia Roberson
- Philippe Taieb
- Michael Takagawa
- Terra Winston
- Johanna Wise
- Debbie Wolter
- Rebecca Zucker
- Complimentary Coaching
- Changing Careers
- Work-Life Integration
- Career Breaks
- Flexible Work
- Encore Careers
- Join a Board
- D&B Hoovers
- Data Axle (ReferenceUSA)
- EBSCO Business Source
- Global Newsstream
- Market Share Reporter
- ProQuest One Business
- RKMA Market Research Handbook Series
- Student Clubs
- Entrepreneurial Students
- Stanford GSB Trust
- Alumni Community
- How to Volunteer
- Springboard Sessions
- Consulting Projects
- 2020 – 2029
- 2010 – 2019
- 2000 – 2009
- 1990 – 1999
- 1980 – 1989
- 1970 – 1979
- 1960 – 1969
- 1950 – 1959
- 1940 – 1949
- Service Areas
- ACT History
- ACT Awards Celebration
- ACT Governance Structure
- Building Leadership for ACT
- Individual Leadership Positions
- Leadership Role Overview
- Purpose of the ACT Management Board
- Contact ACT
- Business & Nonprofit Communities
- Reunion Volunteers
- Ways to Give
- Fiscal Year Report
- Business School Fund Leadership Council
- Planned Giving Options
- Planned Giving Benefits
- Planned Gifts and Reunions
- Legacy Partners
- Giving News & Stories
- Giving Deadlines
- Development Staff
- Submit Class Notes
- Class Secretaries
- Board of Directors
- Health Care
- Sustainability
- Class Takeaways
- All Else Equal: Making Better Decisions
- If/Then: Business, Leadership, Society
- Grit & Growth
- Think Fast, Talk Smart
- Spring 2022
- Spring 2021
- Autumn 2020
- Summer 2020
- Winter 2020
- In the Media
- For Journalists
- DCI Fellows
- Other Auditors
- Academic Calendar & Deadlines
- Course Materials
- Entrepreneurial Resources
- Campus Drive Grove
- Campus Drive Lawn
- CEMEX Auditorium
- King Community Court
- Seawell Family Boardroom
- Stanford GSB Bowl
- Stanford Investors Common
- Town Square
- Vidalakis Courtyard
- Vidalakis Dining Hall
- Catering Services
- Policies & Guidelines
- Reservations
- Contact Faculty Recruiting
- Lecturer Positions
- Postdoctoral Positions
- Accommodations
- CMC-Managed Interviews
- Recruiter-Managed Interviews
- Virtual Interviews
- Campus & Virtual
- Search for Candidates
- Think Globally
- Recruiting Calendar
- Recruiting Policies
- Full-Time Employment
- Summer Employment
- Entrepreneurial Summer Program
- Global Management Immersion Experience
- Social-Purpose Summer Internships
- Process Overview
- Project Types
- Client Eligibility Criteria
- Client Screening
- ACT Leadership
- Social Innovation & Nonprofit Management Resources
- Develop Your Organization’s Talent
- Centers & Initiatives
- Student Fellowships
- Customer Relationship Management
- Forecasting
- Global Distribution
- Healthcare Supply Management
- Inventory Management
- Procurement
- Sales and Operations Planning
- Supply Market Intelligence
- Sustainability
- Transportation Planning
Supply Chain Interdiction: The Mysterious Case of Exploding Pagers
As the world economy became increasingly globalized, supply chains also became more global. As a consequence, never in our industrial economic history had competition become so intense so quickly. North American companies compete not only with other North American companies, but also with companies around the globe. This has resulted in the expansion of the United States economy in many important sectors.
Manufacturing also became global. Commodities created from raw materials hailing from one part of the world, built in factories located in another part of the world, combined and bundled with other commodities located in still other parts of the world, were sold to consumers from Tokyo to Berlin.
Materials, components, and products can cross multiple geographies and regions in their journey through the supply chain, due to different tax structures, logistical efficiencies, and labor arbitrage differences. Therefore, depending on the product, demand, capacity, and other factors, companies can source materials and components for their products from other geographical regions, or may do so from local suppliers. The ability to coordinate with worldwide partners has increased because of the diffusion of the internet. Global sourcing has also increased. The majority of electronics sold in the U.S. are now produced in Asia, not in North America. As supply chains became more complex, however, it also became more difficult to find out exactly where materials, components, and products travelled in their path through the chain because, also by virtue of the internet, nearly anyone could become a seller or buyer at any point along the supply chain.
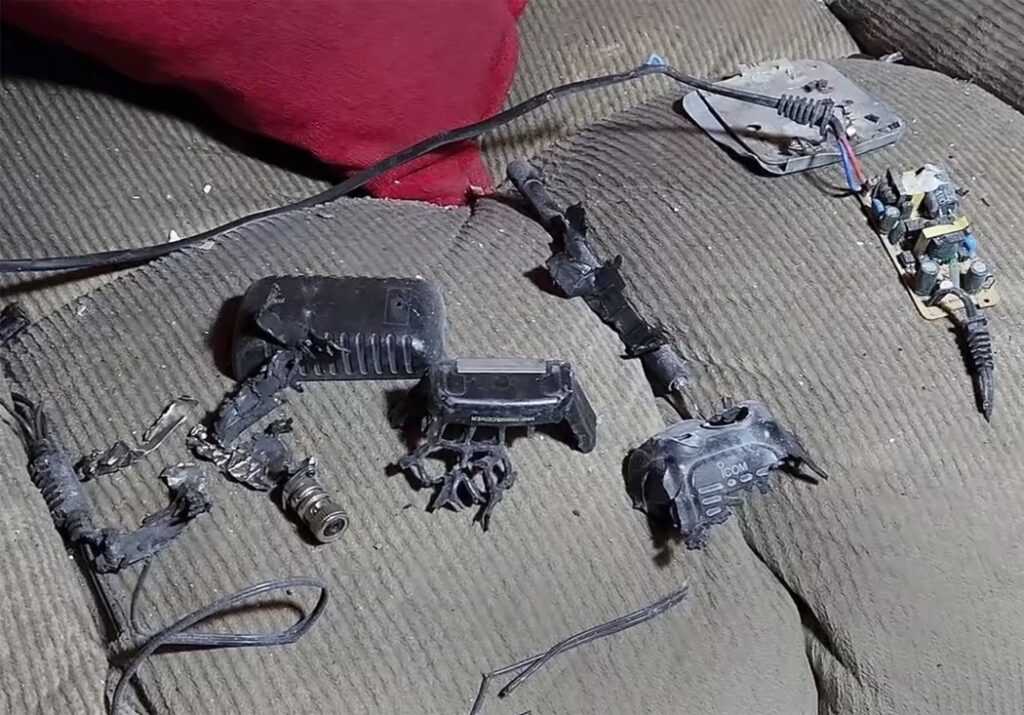
These complex supply chains make it increasingly easy for nefarious activities to be inserted into any point along the chain. This type of activity is called supply chain interdiction, and refers to the activities involved in interfering with the normal, designed processes of any supply chain. Interdiction can result in counterfeits being inserted into the distribution channel, sabotaging products, cyberhacking, data gathering, or any other type of illegal activity.
In the last few years, this potential for interdiction has only escalated, as companies like Amazon and Alibaba have made global competition more important than ever. (This has also led to other problems, such as increased sales of counterfeit products). Moreover, as cost competition has increased, organizations have “outsourced” more of their functions, to lower cost suppliers that are located in areas all over the world. More companies than ever before have outsourced their manufacturing capabilities to organizations called “contract manufacturers.” As Table 1, below, demonstrates, many are now headquartered in Asia. Even those that are headquartered in the United States, including Flextronics, Jabil, and Sanmina, have the majority of their factories in Asia (and some in Eastern Europe).
HonHai Precision Industry (Foxconn) | 1 | 1 | Taiwan |
Pegatron | 2 | 2 | Taiwan |
Flextronics | 3 | 3 | USA |
Jabil | 4 | 4 | USA |
Wistron | 5 | 7 | Taiwan |
Sanmina | 6 | 5 | USA |
Celestica | 7 | 6 | Canada |
New Kinpo Group | 8 | 8 | Taiwan |
USI | 9 | 11 | China |
Venture | 10 | 13 | Singapore |
That contract manufacturers are now predominantly located in Asia reflects not only the shift in manufacturing from Europe and the United States to Asia, but also the shift in the location of the consumption of many finished electronic goods to Asia. In countries such as China, income and discretionary spending have increased at an unprecedented rate since 2000. [1]
- Although these contract manufacturers are located in Asia, they produce and distribute final products for major global brands, including Samsung, Apple, GE, Dell, Ford, Lenovo, Siemens, and other recognizable global brands, both locally and worldwide. With these shifts in global manufacturing, the structure of supply chains has also shifted.
- A few entities like Walmart have achieved near total control over their supply chains. [1] But Walmart is the exception. The vast majority of individual firms, including very large firms, do not have the same market power — and therefore capability — to manage all aspects of their supply chains, particularly since supply chains often include multiple firms with potentially conflicting objectives. Essentially no commodity or upstream component suppliers of which I am aware have such control or capability.
- While Walmart is one instance in which a single, powerful firm took primary responsibility for improving performance across its own supply chain and had the power to do so, nearly all companies in a modern global supply chain will only work with their immediate upstream suppliers and their immediate downstream customers. (This is sometimes referred to as “Tier 1” suppliers/customers.) They rarely have the ability to control or influence parties that are beyond this immediately-adjacent level. A second step removed is, in most cases, where a company’s insight and influence ends. This is particularly the case in industries — like manufacturing of pagers at issue in this case — where there are many competitors and the entities are not sole-source suppliers, but instead compete with other international firms to provide materials, components, or products to the same customer. As competition rises, the ability of any supplier of components to influence the activity of Tier 1 and later users diminishes. Notably, the WSJ reports that Gold Apollo operates in a very competitive space involving a low margin low volume product. As such, for companies in this space, there is often very little visibility and influence beyond “Tier 1” entities in a supply chain. Tier 1 was BAC Consulting, a shell company in Bulgaria, and Tier 2 was Norta Global, in Norway. But even now, it is not clear how these shell companies were tied to the output of pagers.
[1] Yuval Atsmon and Max Magni, “Meet the Chinese Consumer of 2020,” McKinsey Quarterly (March 2012), available at https://www.mckinsey.com/featured-insights/asia-pacific/meet-the-chinese-consumer-of-2020.
[2] Stalk, Evans & Shulman (1992), “Competing on capabilities: The new rules of corporate strategy”, HBR, Vol. 70, no. 2, pp. 57-69.
- China Supply Chain
- Counterfeit Supply Chain
- Director's Blog
- FLOW: How the Best Supply Chains Thrive
More From Supply Chain Resource Cooperative
Five myths about the supply chain heading into 2022, rob handfield lists 10 ways to outsmart the supply chain when holiday shopping, maybe its time for consumers to consume less...market satiation as a new supply chain strategy.
Site Navigation
Latest stories, start your day right, making mattel’s supply chain strong “kenough”: interview with roberto isaias, mattel chief supply chain officer—and cscmp edge keynote speaker—roberto isaias discusses how changes to the toy company’s supply chain planning process helped it handle the pandemic and the spike in sales from the barbie movie..

This story first appeared in the July/August 2024 issue of Supply Chain Xchange, a journal of thought leadership for the supply chain management profession and a sister publication to AGiLE Business Media & Events’ DC Velocity.
Supply chain disruptions don’t always come from negative events like a global pandemic or a natural disaster. Sometimes they come out of positive events such as a spike in sales or an innovation.
In the past four years, the toy company Mattel has faced disruptions on several fronts—both good and bad. Like everyone, Mattel had to deal with the challenges of the Covid pandemic. Then last year, the smash success of the Barbie movie drove sales of movie-related items sky high, putting pressure on its supply chain to keep up.
Fortunately, the company and its chief supply chain officer, Roberto Isaias, have been taking steps for years to transform and better synchronize Mattel’s supply chain operations. This transformative work laid a solid foundation that helped them make savvy decisions in the moment and seize opportunities that both these events offered.
Isaias began his supply chain career at Procter & Gamble, which he calls a “formative” experience and excellent training ground for how to conduct large-scale projects focused on supply chain network planning, network optimization, and strategic planning. He then switched over to the commercial side before joining Mattel in 2002. At Mattel, Isaias, who is from Mexico, held a variety of leadership roles in Latin America prior to his appointment as chief supply chain officer in 2019.
Isaias will be discussing his experience guiding Mattel’s supply chain during his keynote address on Oct. 1 at the Annual CSCMP EDGE Conference in Nashville, Tennessee. DC Velocity Editor at Large Susan Lacefield recently had an opportunity to talk to Isaias and provide a preview of topics that he may be covering.
Q: What were some of the first initiatives that you were involved with when you became chief supply chain officer at Mattel?
A: That was a really exciting time, as the company was in the midst of a turnaround led by our current CEO, Ynon Kreiz. And a lot of the focus was to really restructure our system in ways that [would allow us to] be more profitable. Kreiz is a great boss. He really allows you to make decisions and push the boundaries. So very quickly we were able to reconcile the system and redesign the way we were working.
The biggest changes we made were on the planning side. I call it “synchronizing the supply chain.” For example, we had an algorithm that used inventory turns to calculate production levels at the plant. So we were having a very “nervous” system, where we were making a lot of [production] changes that were really hitting our profitability. But frankly, when you do that in China, it doesn’t make any sense. Because after you turn that fast, you put it on a boat for eight to 10 weeks. So why were you in a hurry? Why don’t you try to keep your productivity?
What we did is say, “Look, we should not be running our manufacturing lines for two or three or four hours, as you do in other businesses like consumer goods. What we need to do is to run our manufacturing lines for days.” That will increase our inventories probably by a day and a half. But frankly, it doesn’t really matter; we’re going to put that on the boat for 10 weeks. If [running our manufacturing lines longer] is going to give us much more productivity, we probably want to do that. So we changed the pattern of how we plan. And that algorithm alone probably gave us 30% more productivity.
The second thing we did is resize our capacity. When every single line is 30% more productive, then your costs also go down, and you don’t need as many factories. As a result, we decided to close some of our factories, particularly in North America. But even with fewer plants, we were [still] able to produce the same amount of product, so a lot of our fixed costs were reduced.
And the third [thing we did] was to make a lot of changes in the way we select an end-of-life for a product. By now, we have reduced probably close to 40% of our SKUs. We used to have a line that was very broad. And as we reduced that, we actually increased our productivity again, reduced our complexity, and sped up inventory turns in the plant. All of that really helped us to work in much better ways. From 2019 to 2023, we have saved about $380 million.
Q: Mattel faced some significant challenges during the pandemic. Could you talk about those challenges and how the work that you had done previously helped you handle them?
A: The pandemic was a crazy time. I think that the work we did systematizing the way we did the production planning in the plants really helped us. Before the pandemic, we pulled production planning out of the plants, so that the production planner was here in the U.S. We have a team that is in a central location, and we have created visibility to all the raw materials and all the components in our [manufacturing resource planning] tool and to our suppliers’ materials.
When we saw the pandemic beginning, there were three things that we did really well. First, we increased our safety inventories in the plants from 30 days to 120 days. We immediately put in orders for electronics, paint, plastic, and pellets. We went to the CFO and said, “Look, this is going to be about $200 million of more inventory. But if we don’t order now and the cost goes up, then we will not be able to survive.”
Our CEO and our CFO were key. They were open [to the recommendation], and they said, “Look, most of it you will use anyway. Of course, it will be a time and a cash flow challenge for the next few months. But after that, if we get it right, we will be able to grow.” It was really lucky that we saw that [trend], and we were really supported by our management team.
The second thing that we did is [ensure] we had that centrality that allows us to make production decisions and react really fast. Sometimes we were changing the production on a daily basis.
And third, our planning person—who has worked in our plants in mainland China and Asia—and myself—who has been here for a long time—we were able to understand the trade dynamics. We knew that if we produce enough and the demand was still high, our customers would take the inventory sooner or later. So [in the summer], they were pausing [orders with us]. But we knew that after that, [our products] would go because they need to sell toys in the winter. So we took the risk of continuing to produce and build our inventory up in China to 300 containers. We took those containers and placed them in basketball courts and football fields we had rented. As soon as our customers’ summer items were gone, they immediately started taking our product, and we were able to grow 20% that year. We hadn’t grown that much in many years.
But again, the CFO, the chief commercial officer, our CEO, and everyone was aligned on how much risk we wanted to take. And it played out well. In our plan, we were supposed to grow 4%, and we ended up growing 20%.
Probably the key pieces were what we did before [the pandemic] to really be prepared and really have a consistent system with enough visibility, and then some smart choices on how to operate. Compared to our peers that produce in China, we were probably the best ones in service and growth.
Q: Did that basis also help you respond to the increase in sales you saw as a result of the Barbie movie?
A: This is incredibly exciting! The Barbie movie has been one of the great events during my career at Mattel. I don’t know if you know, but Mattel was actually the first company that advertised toys on TV. It was during “The Mickey Mouse Club” in the 1950s. That’s what drove the early success of Barbie and Hot Wheels, and the explosion of Mattel as a global company. Now with the Barbie movie, our team and some of the visionaries that we have here really were able to put together a great story with a great director and with great talent.
With this movie, we had two challenges. First, the launch was really tight. Normally we have a lot of time to go see the movie and have the [toy] designers draw their ideas with the movie in place. In this case, we were not able to do that. So our designers and some design developers were on the set. As they were filming the movie, the designers were drawing ideas and creating products. That was completely different from what we did in the past.
We also started with some direct-to-plant development ideas. We took a lot of the product development ideas and sent them to the plant to continue the development process not in the U.S. but in Indonesia. And that really accelerated the development.
Third, we started working around the clock on the production. And once we reached the volume that we were planning to have, we kept producing. This allowed us to hold some of the inventory and then have production capacity later in the year in case demand [exceeded our initial expectations], which actually happened. We were glad that we created some of that inventory early in the year.
Our plants are not completely full the entire year, as we have a very seasonal business. They are completely heavy-loaded from April to September. But they are probably [at] 50% [capacity] the rest of the year. So what we do when we really need to drive volume is we fully pull forward the production. Instead of starting in March or April, when we’re supposed to start, we produce in December, January, February, and that allows us to have some free capacity. Of course, it creates more inventory and more risk. But it allows you to have more of what we call “chasing capacity”—that allows us to really adapt and produce more of what is in demand in the later months of the year. So what we did is we created spare capacity or chasing capacity for that summer, and we’re really happy that we did that. That is the way we actually managed those changes in production. And that’s how we were able to chase the higher-than-expected demand for the movie items.
Q: How did you work with your customers in handling the demand?
A: Our customers were so eager to have the product. We would say, “Well, yeah, I can ship you that. But I will only have [the products] on Sunday, the 7th,” and our customers would say, “Yes! How many trucks do you have?” Or we would say, “We can send it to the store, but people will not get it until June. Is that OK?” And our customers would respond, “Yes. I’ll send a note. Tell me the date; I’ll make it happen.”
The eagerness and the excitement around the movie was great, and our customers were great partners. Our customers have their own schedules; they have a lot of stores and a lot of suppliers they are trying to manage. They have a very hard business to run. I was surprised how flexible, how nice, and how excited they were about the movie. Everyone wanted the product, and everyone wanted the material associated with the movie, and everybody was asking for tickets to the premiere, which were extremely limited!
I would say part of the fun of the story is how flexible our customers were. They were just willing to open their doors and help us drive this on a compressed schedule. Part of the success is not only what we did, it was also that they were extremely helpful. And it was one of the biggest successes that Mattel has had in its history. And now we have a lot of other movies in the pipeline. And that is super exciting!
Infographic: The building blocks of the IoT
A case study: the southern hemisphere's largest automated distribution center, aml launches strikerx mobile computer, htl freight acquires cts logistics, expanding into managed transportation, more stories, three steps toward safer loading docks.
When it comes to your loading docks, safety should be job one.
Occupational Safety and Health Administration (OSHA) data show that a quarter of all industrial accidents happen at loading docks, making this vital, high-activity area a place for vigilance and attention to detail.
“We’re talking about industrial equipment. People don’t get paper cuts here; there can be serious injuries and potential fatalities,” explains Ryan Schaffner, director of sales for loading dock equipment manufacturer McGuire, a division of Systems LLC. Schaffner says there are 7,700 forklift accidents per year at loading docks across the United States: “That’s 21 [incidents] per day. It’s important to protect yourself.”
Protecting employees, vendors, transportation providers, and visitors—anyone who could come into contact with your loading docks—gets a little bit easier when you can identify risks and stay up to date on the latest advances in loading dock systems and equipment. Here are three ways to help ensure your loading docks are as safe as possible.
COMMUNICATE
The biggest accident risk at the loading dock? Early departure of a truck or trailer while a forklift is still inside. The best way to avoid that risk? Good communication and good processes.
“Loading docks are loud, complex environments,” Schaffner explains, noting that in many situations, there’s no clean line of sight or established process for dock workers to communicate with truck drivers coming in and out of the yard every day.
“It’s easy for miscommunication to happen,” he adds. “Ultimately, though, customers [need to] own what happens on their property and in their building. It may be a FedEx driver, but the customer site has to own the safety of the loading and unloading [operations].”
One way to solve the problem is to install a light-communication system that indicates when it’s safe for a truck to enter or leave the dock, and when the driver should stay put. Like traffic signals, dock alerts use red and green lights inside and outside the building—working in opposition—to let both the driver and the forklift operator know the status of the loading or unloading operation. A green light inside indicates it’s safe for the forklift operator to load or unload, and a green light outside lets the driver know it’s safe to pull in or away, for instance. Red lights indicate the opposite.
Truck restraints add another layer of protection and can work in conjunction with light systems. Usually mounted underneath the dock leveler—which is a platform that ensures the safe and smooth movement of goods from the truck to the building—truck restraints hook onto a trailer’s bumper or to a bar underneath the truck, holding it to the building so that the truck can’t pull away without substantial force. Restraints also help eliminate trailer “creep”—which happens when the trailer starts to inch away due to the repetitive motions of the forklifts entering and exiting the trailers. The restraints prevent this and hold the trailer fast to the dock. When the dock leveler is stored and there’s no forklift or worker inside the trailer, a green light tells the driver it’s OK to go.
“Try to increase communication to avoid the incident from occurring,” Schaffner advises, referring to the light system. “The insurance policy is the truck restraint—the physical means of holding you to the building.”
Moving from manual to automated loading dock systems is also a good way to improve safety. Dock levelers offer another useful example: Mechanical systems require workers to manually raise and lower the leveler, putting them in close contact with equipment—which can raise the risk of slip-and-fall accidents, among other dangers. Alternatively, air-powered and hydraulic dock levelers utilize pushbutton controls that allow workers to remain at a safe distance from the truck and leveler, reducing the risk of accidents.
Schaffner says more than half of the warehousing industry uses mechanical systems, so there’s plenty of room to convert to automated protocols where it makes sense. Experts at loading dock equipment maker Rite-Hite agree; in a report on industry trends from early this year, the company listed the automation of labor-intensive tasks as one of the top loading dock trends of 2024.
“… manually lifting a loading dock leveler or bending over to throw open a dock door can be taxing on anyone’s back and body. These repetitive motions can lead to chronic pain that stays with workers long after they’ve punched out for the day. In fact, back injuries account for one in five workplace injuries. And 80% of those injuries are caused by manual material handling that requires twisting, carrying, or extending out to reach something,” Rite-Hite said in its report. “This is more often seen inside the facility, but in the last 10 to 15 years has been addressed at the loading dock with the application of pushbutton controls for dock [leveler] operation.”
Such systems help keep workers at the control box, where they are both ergonomically protected and out of harm’s way.
Automated systems can also help ensure that loading dock operations are handled in the proper sequence each and every day—another key to safety.
“We encourage customers to look at that—how do we protect everyone to make sure it’s the safest operation [and also that] we’re using things in the proper order every single time,” Schaffner says. “We talk a lot about sequence of operation. And the more we encourage [customers] to buy more powered equipment than manual [equipment], the better.”
Leaders at Rite-Hite concur. Advanced loading dock controls can help “bake” safety into the equation by programming equipment to only work in an “interlocked safe sequence of operations,” according to the 2024 trends report. Rite-Hite uses its Dok-Lok system as an example: The sequence of operations begins when the truck backs in and the Dok-Lok becomes engaged with a rear-impact guard, or a wheel-based restraint is engaged with the rear wheels.
“Once the vehicle is secured, the dock barrier can be stored out of the way [and] the overhead door can be opened and the leveler positioned into the trailer bed,” according to the report. “After loading/unloading, the restraint is not allowed to disengage the trailer until the leveler is taken out of the trailer and stored safely, [the] dock door [is] closed, and [the] safety barrier [is] engaged across [the] dock opening.”
McGuire/Systems LLC offers similar solutions.
“Your restraint has to be engaged before you open the door, [so there is] always a protective layer there,” Schaffner says. “Likewise, you can’t engage the dock leveler until the door is in a fully open position.”
The ultimate goal? A safe and secure loading dock.
CEOs: Our supply chains have a resiliency problem
Cscmp calls on white house to prevent port strike, descartes buys cargo theft prevention firm mycarrierportal for $24 million, raymond corp. boosts energy solutions with new battery plant, kuehne+nagel opens 10th healthcare logistics facility in canada, deutsche bahn to sell db schenker to dsv, don’t miss out, cma cgm to acquire nearly half of brazilian port terminal operator.
The French container shipping and logistics provider CMA CGM Group has agreed to acquire nearly half of Santos Brasil Participações S/A , a Brazilian multi-terminal operator that manages South America’s largest container terminal, which is located at the Port of Santos.
CMA CGM will purchase a 48% stake in the company from its current owner, Opportunity Funds. Santos Brasil manages a portfolio of 8 assets on the Brazilian coast, including 3 Container Terminals, 1 Vehicle Terminal, 1 Liquid Bulk Terminal, and 3 Logistic Facilities. These assets are located in the Ports of Santos, Imbituba, Vila do Conde, Itaqui and in Sao Paulo.
Once the acquisition closes, CMA CGM intends to further develop its line calls in the various Brazilian terminals and further improve its offering to Brazilian exporters and importers, thereby responding to increasing demand and better addressing consumer needs.
The move will also enable CMA CGM to offer “seamless connections” between Europe, Asia, North America, and the Caribbean, thus solidifying Brazil's position as a key hub in the group’s worldwide operations and reinforcing synergies with its MERCOSUL Line affiliate.
The deal marks CMA CGM’s latest move to expand its port holdings, reinforcing its position as a leading global multi-user terminal operator with investments in approximately 60 terminals worldwide, the company said.
“I am pleased that the CMA CGM Group has concluded this strategic agreement for the acquisition of Santos Brasil, which operates five terminals in Brazil, including the largest container terminal in the Port of Santos, handling 40% of Brazilian volumes, as well as a logistics company. This significant investment reflects our commitment to strengthening our partnership with Brazil and supporting its growth in the coming years,” Rodolphe Saadé, CEO of CMA CGM Group, said in a release.
Watchdog group says FAA should fix air traffic control systems
A government watchdog group is calling for the Federal Aviation Administration (FAA) to take “long-overdue” action to modernize the nation’s aging, unreliable air traffic control systems, according to the Center for Transportation Policy (CTP).
The group made its demand in the wake of a report released today by the Government Accountability Office (GAO) which found that 51 of the FAA’s 138 air traffic control information systems are unsustainable, citing outdated functionality, a lack of spare parts, and more.
The GAO report also said that over half of those unsustainable systems are especially concerning, but the FAA has been slow to modernize. Some system modernization projects won't be complete for another 10 to 13 years. But the FAA also doesn't have plans to modernize other systems in need—3 of which are at least 30 years old, the GAO report found.
“News out of the Government Accountability Office highlighting the vulnerabilities of our air traffic control systems is disturbing,” said Jackson Sheldelbower, executive director of the Center for Transportation Policy (CTP). “Pete Buttigieg and the Department of Transportation need to get their priorities straight. We’re urging federal officials to fast-track the repairs and modernization projects necessary to bring air travel into the twenty-first century.”
Study: bridges may need more protection from ship collisions
Bridges in New York, California, and Georgia are among U.S. spans with the most traffic from the largest ships, leaving them at potential risk from collisions, according to a report from Johns Hopkins University that follows the collapse of Baltimore’s Key Bridge in March when it was struck by a drifting containership.
The team created the risk assessment model because they believe that chances are high for another such incident, and that risk to the Key Bridge amid modern shipping traffic had been underestimated . Now, the team hopes that decisionmakers can strategically direct safety investments to bridges most in need.
“We’re asking, ‘What is the probability of a very large ship taking out another bridge?’ and to get at that question, the first thing we have to do is understand the actual ship traffic under major bridges across the U.S.,” Michael Shields, a Johns Hopkins University engineer specializing in risk assessment and lead investigator of the National Science Foundation supported study, said in a release.
“This traffic data suggests a relatively small number of bridges see a disproportionate amount of the largest ship traffic. It’s very clear where the heavy traffic is happening and these bridges should be prioritized for more careful and rigorous risk analysis,” Shields said.
To create the study, researchers used data mining techniques to identify the nation’s bridges that are the most vulnerable to a similar strike. First, they collected six years of U.S. Coast Guard data—logs detailing the precise location, heading, speed, and status of every ship traveling through the country’s waters on a minute-by-minute basis. Then they cross-referenced the geolocated shipping information with port data and bridge data from the National Bridge Inventory to determine which large ships passed under bridges. Finally, they built a program to analyze that data set to assess large-ship traffic under more than 200 major U.S. bridges.
The results show that three bridges had—by far—the most traffic from the very largest ships: The Verrazzano-Narrows Bridge in New York City, the Talmadge Memorial Bridge in Georgia, and two San Francisco Bay Area bridges. In addition, bridges with the most traffic from large (but not necessarily the very largest) ships include Houston’s Fred Hartman Bridge and several bridges along the Mississippi River including the Crescent City Connection in New Orleans. Meanwhile, the Francis Scott Key Bridge ranked among the top 10 bridges in very large ship traffic, with on average one ship longer than 300 meters (the size of the Dali) passing under it per day.
Shields cautioned that high ship traffic alone doesn’t necessarily mean a bridge is at high risk for collisions. Other variables that play a role include local shipping channel conditions, along with existing shipping safety practices, and individual bridge protections.
Kodiak Robotics to hitch Wabash trailers to its self-driving trucks
Autonomous trucking technology provider Kodiak Robotics Inc. has agreed to use a trailers as a service (TaaS) program from the transportation, logistics and distribution equipment provider Wabash , thus gaining access to a fleet of trailers nationwide.
According to Indiana-based Wabash, its TaaS offering differs from traditional leasing because it ensures minimal downtime by providing a holistic solution that supports the full lifecycle of the trailer, from acquisition to maintenance and uptime management.
In addition to its TaaS service, Wabash makes products including: dry freight and refrigerated trailers, flatbed trailers, tank trailers, dry and refrigerated truck bodies, structural composite panels and products, trailer aerodynamic solutions, and specialty food grade processing equipment.
In turn, California-based Kodiak will focus on further developments to “Kodiak Driver,” its autonomous technology. The company last month said it had surpassed 50,000 miles of autonomous long-haul trucking by working in collaborations with other companies such as supply chain solutions provider J.B. Hunt Transport Services Inc. and tire and sustainable mobility vendor Bridgestone Americas.
- Case studies
- Call for contributions

From Dr. Paolo Trucco and Dr. Alessandra Negri.
Headquartered in California, Mattel Inc. designs, manufactures, and markets a broad variety of recreative products. The company employs nearly 30,000 employees and its yearly sales in 2016 amounted to about 4,930 million euros, with an operating income of 469 million. Mattel’s principal manufacturing facilities are in Canada, China, Indonesia, Thailand, Malaysia and Mexico, but it also relies on third-party manufacturers all around the world. From August to September 2007, Mattel recalled more than 1.5 million toys due to non-approved surface paint containing high quantity of lead. Since the US regulatory established that the surface coatings cannot exceed 0.06% lead by weight, the company had previously given manufacturers in China a list of paint suppliers that they could use. However, a subcontractor employed an unauthorized supplier, exceeding the limit. Lead-based paint is dangerous for children because its ingestion causes learning and behavioral problems, slow muscle and bone growth, hearing loss and brain damage. Therefore, consumers were asked to return products in exchange for a voucher valid for a replacement toy. After the event, the Chinese government revoked export license to the subcontractor and Mattel tightened its product-monitoring efforts. Thanks to its experience with recalls, the company smoothly faced all aspects of the incident, giving accurate, quick and efficient information about the recall to the public and reassuring consumers. It also created a website dedicated to the recall. In addition, the company’s effective communication strategy was fundamental: it placed notifications in 20 languages on its website, sent letters to its customers and retailers, manned a hotline, placed full-page ads in major newspapers, and worked closely with the media.
Even though the low impact of the event on Mattel’s annual results was determined mainly by its ability to manage a good communication plan, some supply chain complexity drivers played an important role in the recall, as well. First, having facilities worldwide, the company could slow down shipments out of Asia, flexibly relying on other plants. Secondly, partially covering layers of the supply chain on the demand side allowed the company to prevent affected toys from reaching end consumers, by stopping them in distribution centers and contracting retailers. Thus, high complexity of the supply chain on the demand side, thanks to the collaboration with actors of the distribution channels, positively contributed to reducing incidents. However, the large number of actors involved in Mattel’s supply chain also revealed an issue of visibility of the supply chain, reducing the possibility to quickly identify non-compliant suppliers. Therefore, the internal structural complexity of the supply chain in this case achieved mixed results. Internal dynamic complexity drivers allowed for both flexibility and velocity. Being used to investing in initiatives to improve the supply chain, the company could manage the supply reconfiguration determined by the incident. Furthermore, this spirit of constant improvement allowed Mattel to review its safety procedures and extend its product testing programs.
RELATED ARTICLES MORE FROM AUTHOR

From News to Crisis: Key Factors in Event Escalation

The tenuous boundary between reality and perceptions in crisis management

Silence Makes Noise: from Sound Design to Crisis Communication

When the party’s over

After the Quake: some Reflection
Leave a reply cancel reply.
Log in to leave a comment
A deep dive into BP’s Deepwater Horizon Spill: a case study
High cost of racism in high fashion: a case study on dolce and gabbana’s..., domino’s pizza, the toss and turn, netflix’s way: innovating resilience.

When you visit a website, it may store or retrieve information on your browser, mainly in the form of cookies. Check your personal cookie services here.
- wordpress_test_cookie
- wordpress_logged_in_
- wordpress_sec
- wordpress_gdpr_cookies_allowed
- wordpress_gdpr_cookies_declined
- wordpress_gdpr_allowed_services
- __wpdm_client
Application: Managing Product Recalls—the Case of Mattel, Inc.
Cite this chapter.
- ManMohan S. Sodhi 3 &
- Christopher S. Tang 4
Part of the book series: International Series in Operations Research & Management Science ((ISOR,volume 172))
7506 Accesses
In addition to supply chain risks that occur before sales, companies need to think about the risks that may occur after sales. Specifically, product recalls due to safety considerations for consumers can put companies at risk. This chapter deals with product safety and recall and examines how companies manage their product recall process and implement ways to mitigate product risks in the future. We use the case of Mattel, Inc. and its toy recalls in 2007 to illustrate handling of the product recall process.
This is a preview of subscription content, log in via an institution to check access.
Access this chapter
Subscribe and save.
- Get 10 units per month
- Download Article/Chapter or eBook
- 1 Unit = 1 Article or 1 Chapter
- Cancel anytime
- Available as PDF
- Read on any device
- Instant download
- Own it forever
- Compact, lightweight edition
- Dispatched in 3 to 5 business days
- Free shipping worldwide - see info
- Durable hardcover edition
Tax calculation will be finalised at checkout
Purchases are for personal use only
Institutional subscriptions
Unable to display preview. Download preview PDF.
Author information
Authors and affiliations.
Cass Business School, City University, London, UK
ManMohan S. Sodhi
Anderson School of Management, University of California, Los Angeles, Los Angeles, CA, USA
Christopher S. Tang
You can also search for this author in PubMed Google Scholar
Rights and permissions
Reprints and permissions
Copyright information
© 2012 Springer Science+Business Media, LLC
About this chapter
Sodhi, M.S., Tang, C.S. (2012). Application: Managing Product Recalls—the Case of Mattel, Inc.. In: Managing Supply Chain Risk. International Series in Operations Research & Management Science, vol 172. Springer, Boston, MA. https://doi.org/10.1007/978-1-4614-3238-8_12
Download citation
DOI : https://doi.org/10.1007/978-1-4614-3238-8_12
Publisher Name : Springer, Boston, MA
Print ISBN : 978-1-4614-3237-1
Online ISBN : 978-1-4614-3238-8
eBook Packages : Business and Economics Business and Management (R0)
Share this chapter
Anyone you share the following link with will be able to read this content:
Sorry, a shareable link is not currently available for this article.
Provided by the Springer Nature SharedIt content-sharing initiative
- Publish with us
Policies and ethics
- Find a journal
- Track your research
Blueberries as a Case Study: Improved Measurement of FLW in the Supply Chain using Trade Data and Analytics

Share this content:
In the contemporary global economy, the journey of food from farm to fork is a complex one. The process often spans continents and can entail multiple phases of storage and transportation. Ensuring that food maintains its quality throughout this journey is becoming more significant as our world becomes more interconnected. A major challenge in this context is dealing with food loss and waste (FLW), which happens at various points along the supply chain. An efficient method to tackle this problem could be utilizing global trade data to assess FLW, particularly for high-value commodities such as blueberries.
The Increasing Significance of Blueberries in the Global Market
The global blueberry market is an evolving sector, currently valued at USD 10.4 billion and expected to reach USD 13.4 billion by 2027. Blueberries are deemed the second most economically significant soft fruit worldwide. 95 percent of blueberry exports are transported via ocean freight and are often shipped over long supply chains. These lengthy supply routes often lead to food loss.
Using Trade Data to Measure Food Loss and Waste
An inventive approach to gauging FLW, currently in its initial research phases, involves examining discrepancies in global trade data, comparing the export quantities declared by exporting nations with the import quantities logged by importing nations to offer a window into the losses occurring during transit. This tactic could offer a clearer picture of where and when food loss happens and could allow for tailored measures to reduce it efficiently.
For example, in the trade of blueberries between Peru and the United States—Peru being the world’s largest exporter and the US its largest importer—trade data revealed an average loss of 8.49 percent in the 2022/23 season. This figure translates to over 17,400 kilograms of blueberries lost during transit. There were comparable trends in the trade between Peru and the Netherlands where losses amounted to almost 13.18 percent. These losses emphasize the importance of improving logistics and handling procedures across the supply chain.

Potential Pitfalls
The data reveals a consistent discrepancy where Canadian blueberry imports consistently exceed US exports across all observed years. This pattern suggests an overestimation of imported amounts or an underestimation of export numbers that could indicate potential data recording discrepancies on either end of the trade relationship. Importantly the difference between imports and exports has grown over time with significant variations noticeable, in recent years. The increasing gap underscores the importance of reviewing trade information and indicates possible challenges with the consistency of trade reporting methods, between the United States and Canada in the context of Blueberry trade.

Benefits of using the Global Trade Data Methodology
The use of trade data to gauge FLW could offer several key benefits:
- Efficiency and Cost-Effectiveness: Typical methods of measuring food loss often rely on costly surveys or inspections. On the other hand of the spectrum, trade data could be a convenient and economical means of tracking food movements across borders.
- Comprehensive Coverage: Trade data encompasses an array of products and regions, offering a complete picture of global food supply chains using the Harmonized Shipping Code (HS) system. This standardized approach allows for consistent and comparable measurements of FLW.
- Actionable Insights: Insights that can guide targeted strategies to reduce waste are crucial. For instance, improvements in cold chain logistics or the introduction of more resilient varieties of blueberries could significantly reduce losses, thereby improving both profitability and sustainability.
Challenges
Utilizing trade data to assess FLWs has potential. However various obstacles need to be overcome to fully leverage its benefits.
- Inconsistencies in Data : The precision of trading data may differ based on the reporting practices of different countries. Discrepancies can distort results and should be rectified through standardized reporting practices.
- Mechanics of FLW : To improve the reliability of FLW measurements, it is essential to delve deeper into the intricacies of food loss during transportation. Engaging with government agencies, industry participants, and logistics providers can shed light on the underlying causes of these losses resulting in better data collection practices.
The use of trade data to assess FLW is still a nascent concept, but the potential for its expansion could be vast. Broadening this research to include more countries and a wider array of commodities could lead to deeper insights into the viability of this approach to measure FLW on a global scale. Moreover, examining data disaggregated by season or region could reveal patterns indicating certain periods or places susceptible to losses. Collaboration with organizations, government entities and industry stakeholders could be highly beneficial in supporting this endeavor. By harnessing this data, it could be possible to uncover fresh insights into the dynamics of food distribution, identify areas for improvement, and introduce measures to minimize FLW. In light of the global concerns around food security and sustainability, it is crucial to recognize the significance of pioneering strategies such as this one. With continued research and collaboration, the future of FLW measurement looks promising and presents an opportunity to make a substantial impact in curbing food wastage worldwide.
More on This Topic from AgriLINKS
Food loss and waste reduction and affordability of safe, nutritious diets, investing in up-and-coming cocoa markets for sector sustainability, how can africa facilitate sps investment and improve outcomes for food safety, fews net scientists: entire ukraine canal system vital for farm irrigation ‘dried up’ after dam breach.
- Food Loss and Waste
- Markets and Trade
Search Agrilinks
- My drafts and published content
Contribute To Agrilinks
- Add an event
Subscribe to receive our bi-weekly newsletter featuring the latest and greatest Agrilinks content.
You'll also receive invitations to upcoming Agrilinks webinars and other special announcements. We won't share your email address and you can unsubscribe at any time.
We use cookies on our website to evaluate site performance and improve your experience. Click " Accept " if you agree to the use of these cookies, or more information to learn about how we manage information on our site.

- Order Status
- Testimonials
- What Makes Us Different
Unsafe for Children: Mattels Toy Recalls and Supply Chain Management Harvard Case Solution & Analysis
Home >> Supply Chain Management Cases >> Unsafe for Children: Mattels Toy Recalls and Supply Chain Management
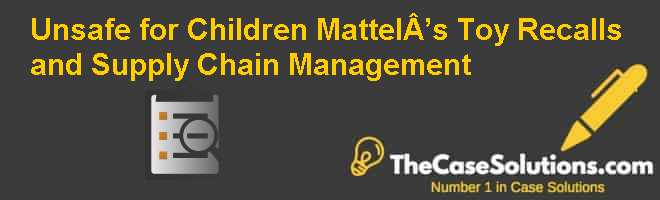
Unsafe for Children: Mattel’s Toy Recalls and Supply Chain Management
Questions Analysis
Question No.1: Why do companies outsource?
There are several reasons for the companies to outsource some of their non-core business functions. Outsourced company will become a strategic partner who will be coordinating with the company. It has many advantages and helps the company to concentrate on their main business rather than distracting their efficiencies in different directions. Nowadays, companies are focusing to give value addition on their core business products. Hence they need to concentrate solely on it, that’s why companies outsource some of their non-core items or their logistics network to any other company by establishing strategic partnership between them.
Sometimes companies outsource because that company have expertise in that business area. For example, NATO and US armed forces have contracted with Maersk Line to outsource their logistics network globally. The reason behind this outsourcing is because providing logistics solution is a core business of Maersk Line and it can do much better comparatively with US armed forces. Outsourcing can help to bring expertise from the outsourced company.
Another reason behind the outsourcing can be the lack of resources in a company, which lead it to outsource to be performed better by an outsourced company. Sometimes companies based in the countries where cost of production is high move some of their functional areas to the low-cost production countries through outsourcing another company mostly for its non-core business.
Outsourcing can help to reduce the excess capital expenses and a company will not need to invest in its non-core business through partnering with other company. Furthermore, it will help a company to improve its overall services on their core areas rather than wasting time and capital on other non-core businesses. In short, outsourcing will lead a company to reduce risks by focusing only on their core functions. Nowadays most companies are trying to improve their main business areas rather than to diversify in other functional activities.
Question No.2: What were the primary causes of Mattel’s recall problem? Were these the result of outsourcing?
There were many issues which became the primary cause of Mattel recalling its goods. There were initially two problems in the Mattel’s toys which were lead excess paint and defective design. According to the recalling volume of Mattel’s goods, most were recalled due to defective design in which small magnets were attached that could become loose. While on the other side, recalling of goods due to excess lead was comparatively low with the defective design. The reason behind the defective design was simply due to the company’s product development process and this had to be focused by them.
Though the units of recalling excess lead paint was comparatively low but it destroyed the company’s image. The reason of excess lead in their products was due to the problem in its supply chain network. Mattel had outsourced Chinese vendors for their non-core business functions, which subcontracted other vendors for paints. Mattel was unaware about the third vendor. Mattel had allowed the vendors to take paints from certified suppliers but many vendors provided false certification and started supplying untested paints which resulted in lead containing toys.
Another problem which they were facing was regarding the pricing strategy. Production cost in US was significantly very high as related with China which saved almost 40 percent of the production cost. The problem was not with outsourcing but it was in their supply chain management. Contracted vendor of Mattel had subcontracted unintentionally with other fake-made documented vendors, which were supplying excess amount of lead in the paints.
Question No. 3: Focusing on the supply chain causes of the recall; what are the factors that lead to suppliers using lead paint. Do you believe that Mattel can control this in future?
The subcontractors were not certified suppliers and had made fake documentation regarding the certification. They started providing excess lead paints and both the immediate vendor as well as Mattel was unaware of it. Lead was cheaper which comparatively resulted in 30 – 60 percent saving as compared to the paint that did not have lead. Chinese vendors already had small profit margins, uncertified suppliers with fake documentation; hence it started using lead in paints to reduce their costs.
Mattel could allow its vendors to subcontract with suppliers , which had to be ISO certified. Still there should be proper testing system to assure the quality of the paint. Vendors should check frequently for the lead containing paints, which can be checked by different lead checking machines. Vendor should verify the certification of..........................
This is just a sample partial case solution. Please place the order on the website to order your own originally done case solution.
In August and September 2007, Mattel made a number of product recalls, totaling more than 20 million toys. Recalls were excessive for lead and magnets that could become loose. All of the recalled toys were made in China. Mattel recalls on the heels of a number of high-profile security problems with Chinese imports, including contaminated pet food and toothpaste, defective tires, and lead-painted toys. Recalls provoked sharp criticism in Mattel and its Chinese supply chain, despite the fact that more than 85 percent of the recalled toys were associated with the design problems (magnets), and not due to improper production (use of lead-based paint). Case provides a basis for discussion of outsourcing and supply chain management. The basic manufacturing process is fairly simple toy, providing a forum to discuss these issues without complications advanced manufacturing or supply chain involved. In this case, supply chain defects, such as the use of lead paint suppliers, can have serious consequences. Supply chain should be designed to prevent these defects. The case allows a discussion of why the company outsourcing, supply chain management and the proper use of inspection and testing. It also provides the opportunity to learn the answer to the crisis, and the relationship between the company and the government. "Hide by Hau Lee, Mitchell M. Tseng, David W. Hoyt Source: Stanford Graduate School of Business 20 pages . Publication Date: September 15, 2008. Prod. #: GS63-PDF-ENG
Related Case Solutions & Analyses:
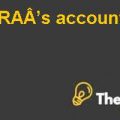
Hire us for Originally Written Case Solution/ Analysis
Like us and get updates:.
Harvard Case Solutions
Search Case Solutions
- Accounting Case Solutions
- Auditing Case Studies
- Business Case Studies
- Economics Case Solutions
- Finance Case Studies Analysis
- Harvard Case Study Analysis Solutions
- Human Resource Cases
- Ivey Case Solutions
- Management Case Studies
- Marketing HBS Case Solutions
- Operations Management Case Studies
- Supply Chain Management Cases
- Taxation Case Studies
More From Supply Chain Management Cases
- WoodSynergy Inc.: Integrating IT into the Supply Chain
- Kamakura Ironworks Co. Ltd.
- Instill Corp.: Improving the Food Service Industry Supply Chain
- Best Value Supply Chains: Key Competitive Weapon for the 21st Century
- Numico (B): Transforming the Supply Chain to Support New Realities
- McDonalds India: Optimizing the French fries supply chain
- Designing the Soft Side of Customer Service
Contact us:

Check Order Status
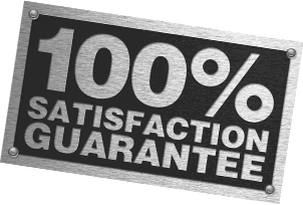
How Does it Work?
Why TheCaseSolutions.com?


IN ONLINE CASE STUDY
For free cases and projects including exciting deals please register yourself .
Free Unsafe for Children: Mattel's Toy Recalls and Supply Chain Management Case Study Solution | Assignment Help
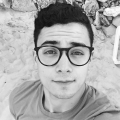
Harvard Case - Unsafe for Children: Mattel's Toy Recalls and Supply Chain Management
"Unsafe for Children: Mattel's Toy Recalls and Supply Chain Management" Harvard business case study is written by Hau Lee, Mitchell M. Tseng, David W. Hoyt. It deals with the challenges in the field of Operations Management. The case study is 20 page(s) long and it was first published on : Sep 15, 2008
At Fern Fort University, we recommend that Mattel implement a comprehensive, multi-faceted strategy to address its supply chain vulnerabilities and restore consumer trust. This strategy will focus on strengthening its supply chain management through robust quality control , risk management , and transparency initiatives. Key elements include:
- Revamping its product development and sourcing processes to prioritize safety and compliance.
- Investing in advanced technology and analytics for real-time monitoring and predictive analysis.
- Establishing a dedicated team for supply chain risk management to proactively identify and mitigate potential issues.
- Implementing a robust communication strategy to ensure transparency with consumers and stakeholders.
2. Background
Mattel, a global leader in the toy industry, faced a series of high-profile toy recalls in the mid-2000s due to safety concerns. These recalls significantly damaged the company?s reputation, leading to financial losses and a decline in consumer trust. The case study highlights the critical importance of supply chain management in ensuring product safety and maintaining brand integrity.
The main protagonists in this case study are:
- Mattel: A global toy manufacturer facing the challenge of managing a complex supply chain and ensuring product safety.
- Consumers: The primary stakeholders affected by the recalls, who demand safe and high-quality products.
- Suppliers: The network of manufacturers and subcontractors responsible for producing Mattel?s toys, who play a crucial role in the overall quality and safety of products.
3. Analysis of the Case Study
This case study can be analyzed through the lens of operations strategy , focusing on the following key areas:
- Supply Chain Management: Mattel?s supply chain was characterized by a complex network of suppliers, many of whom were located in developing countries with varying levels of regulatory oversight. This complexity made it challenging to maintain consistent quality control and monitor safety standards throughout the production process.
- Quality Management: The recalls highlighted significant weaknesses in Mattel?s quality management system. The company relied heavily on outsourcing production, which made it difficult to ensure consistent quality and compliance across its entire supply chain.
- Risk Management: Mattel lacked a robust risk management framework to proactively identify and mitigate potential safety issues. The company?s reactive approach to recalls demonstrated a need for a more proactive and comprehensive risk assessment process.
- Communication & Transparency: The recalls exposed a lack of transparency in Mattel?s communication with consumers and stakeholders. This lack of transparency further eroded consumer trust and damaged the company?s reputation.
4. Recommendations
To address these challenges, Mattel should implement the following recommendations:
1. Strengthen Supply Chain Management:
- Centralized Control: Establish a centralized team responsible for managing the entire supply chain, ensuring consistent quality control and compliance across all suppliers.
- Supplier Selection & Monitoring: Develop a rigorous supplier selection process that prioritizes safety, quality, and ethical practices. Implement robust monitoring systems to ensure ongoing compliance with Mattel?s standards.
- Supplier Training & Development: Invest in supplier training programs to improve their understanding of safety regulations, quality standards, and Mattel?s expectations.
- Technology & Analytics: Implement advanced technology and analytics solutions to track materials, monitor production processes, and identify potential risks in real-time.
2. Enhance Quality Management:
- Robust Quality Control: Implement a multi-layered quality control system that includes in-process inspections, final product testing, and independent audits.
- Total Quality Management (TQM): Embrace a culture of continuous improvement through TQM principles, empowering employees at all levels to identify and address quality issues.
- Six Sigma: Implement Six Sigma methodologies to reduce defects, minimize variability, and improve overall product quality.
3. Implement a Proactive Risk Management Framework:
- Risk Assessment & Mitigation: Conduct regular risk assessments to identify potential safety hazards and develop mitigation plans.
- Scenario Planning: Develop contingency plans for potential disruptions, including product recalls, supplier issues, and natural disasters.
- Early Warning Systems: Establish early warning systems to monitor industry trends, regulatory changes, and potential safety issues.
4. Foster Transparency & Communication:
- Open Communication: Be transparent with consumers and stakeholders about product sourcing, manufacturing processes, and safety measures.
- Proactive Communication: Communicate proactively about potential issues, even if they are not yet confirmed, to maintain trust and manage expectations.
- Social Media Engagement: Utilize social media platforms to engage with consumers, address concerns, and build a positive brand image.
5. Basis of Recommendations
These recommendations are based on the following considerations:
- Core Competencies: Strengthening its supply chain management is crucial to Mattel?s core competency of producing safe and high-quality toys.
- External Customers: The recommendations prioritize consumer safety and satisfaction, which are essential for maintaining customer loyalty.
- Internal Clients: The recommendations aim to empower employees and suppliers to actively contribute to quality and safety improvements.
- Competitors: By implementing these recommendations, Mattel can differentiate itself from competitors by demonstrating a commitment to safety and transparency.
- Attractiveness: The financial benefits of these recommendations include reduced recall costs, improved brand reputation, and increased consumer trust, leading to higher sales and profitability.
6. Conclusion
By implementing these recommendations, Mattel can transform its supply chain into a strategic asset that enhances product safety, strengthens brand reputation, and drives long-term growth. The company must prioritize transparency, accountability, and continuous improvement to regain consumer trust and maintain its position as a leader in the toy industry.
7. Discussion
Other alternatives include:
- Outsourcing all production: While this could reduce costs in the short term, it could also lead to a further loss of control over quality and safety.
- Focusing on domestic production: This could improve control but may increase costs and limit access to specific materials and expertise.
Key assumptions:
- Commitment to change: Mattel must be committed to implementing these recommendations and making the necessary investments in technology, training, and personnel.
- Supplier cooperation: Suppliers must be willing to collaborate and comply with Mattel?s new standards.
- Consumer acceptance: Consumers must be receptive to Mattel?s efforts to rebuild trust and transparency.
8. Next Steps
To implement these recommendations, Mattel should:
- Phase 1 (Short-term): Establish a centralized supply chain management team, conduct a comprehensive risk assessment, and develop a communication strategy.
- Phase 2 (Mid-term): Implement technology solutions for real-time monitoring, develop supplier training programs, and conduct pilot projects for Six Sigma and TQM initiatives.
- Phase 3 (Long-term): Continuously evaluate and refine the supply chain management system, expand the use of technology and analytics, and build a culture of continuous improvement.
By taking these steps, Mattel can transform its supply chain into a strategic advantage, ensuring the safety and quality of its products while regaining the trust of its consumers.
Hire an expert to write custom solution for HBR sales case study - Unsafe for Children: Mattel's Toy Recalls and Supply Chain Management
Case description.
In August and September 2007, Mattel made a series of product recalls, totaling more than 20 million toys. The recalls were for excessive lead and for magnets that could become loose. All of the recalled toys had been made in China. The Mattel recalls followed on the heels of a number of high profile safety problems with Chinese imports, including contaminated pet food and toothpaste, defective tires, and lead-painted toys. The recalls sparked intense criticism of Mattel and its Chinese supply chain, despite the fact that more than 85 percent of the recalled toys were due to design problems (magnets), not the result of improper manufacturing (use of lead paint). The case provides a basis for discussion of outsourcing and supply chain management. The basic toy manufacturing process is fairly simple, providing a forum for discussing these issues without the complication of advanced manufacturing technology or an involved supply chain. In this case, supply chain defects, such as the use of lead paint by vendors, can have severe consequences. The supply chain must be designed to prevent these defects. The case enables discussion of why companies outsource, managing a supply chain, and the appropriate use of inspection and testing. It also provides the opportunity to examine response to a crisis situation, and the relationship between a company and government.
🎓 Struggling with term papers, essays, or Harvard case studies? Look no further! Fern Fort University offers top-quality, custom-written solutions tailored to your needs. Boost your grades and save time with expertly crafted content. Order now and experience academic excellence! 🌟📚 #MBA #HarvardCaseStudies #CustomEssays #AcademicSuccess #StudySmart Write my custom case study solution for Harvard HBR case - Unsafe for Children: Mattel's Toy Recalls and Supply Chain Management
Unsafe for Children: Mattel's Toy Recalls and Supply Chain Management FAQ
What are the qualifications of the writers handling the "unsafe for children: mattel's toy recalls and supply chain management" case study.
Our writers hold advanced degrees in their respective fields, including MBAs and PhDs from top universities. They have extensive experience in writing and analyzing complex case studies such as " Unsafe for Children: Mattel's Toy Recalls and Supply Chain Management ", ensuring high-quality, academically rigorous solutions.
How do you ensure confidentiality and security in handling client information?
We prioritize confidentiality by using secure data encryption, access controls, and strict privacy policies. Apart from an email, we don't collect any information from the client. So there is almost zero risk of breach at our end. Our financial transactions are done by Paypal on their website so all your information is very secure.
What is Fern Fort Univeristy 's process for quality control and proofreading in case study solutions?
The Unsafe for Children: Mattel's Toy Recalls and Supply Chain Management case study solution undergoes a rigorous quality control process, including multiple rounds of proofreading and editing by experts. We ensure that the content is accurate, well-structured, and free from errors before delivery.
Where can I find free case studies solution for Harvard HBR Strategy Case Studies?
At Fern Fort University provides free case studies solutions for a variety of Harvard HBR case studies. The free solutions are written to build "Wikipedia of case studies on internet". Custom solution services are written based on specific requirements. If free solution helps you with your task then feel free to donate a cup of coffee.
I’m looking for Harvard Business Case Studies Solution for Unsafe for Children: Mattel's Toy Recalls and Supply Chain Management. Where can I get it?
You can find the case study solution of the HBR case study "Unsafe for Children: Mattel's Toy Recalls and Supply Chain Management" at Fern Fort University.
Can I Buy Case Study Solution for Unsafe for Children: Mattel's Toy Recalls and Supply Chain Management & Seek Case Study Help at Fern Fort University?
Yes, you can order your custom case study solution for the Harvard business case - "Unsafe for Children: Mattel's Toy Recalls and Supply Chain Management" at Fern Fort University. You can get a comprehensive solution tailored to your requirements.
Can I hire someone only to analyze my Unsafe for Children: Mattel's Toy Recalls and Supply Chain Management solution? I have written it, and I want an expert to go through it.
🎓 Struggling with term papers, essays, or Harvard case studies? Look no further! Fern Fort University offers top-quality, custom-written solutions tailored to your needs. Boost your grades and save time with expertly crafted content. Order now and experience academic excellence! 🌟📚 #MBA #HarvardCaseStudies #CustomEssays #AcademicSuccess #StudySmart Pay an expert to write my HBR study solution for the case study - Unsafe for Children: Mattel's Toy Recalls and Supply Chain Management
Where can I find a case analysis for Harvard Business School or HBR Cases?
Which are some of the all-time best harvard review case studies.
Some of our all time favorite case studies are -
Can I Pay Someone To Solve My Case Study - "Unsafe for Children: Mattel's Toy Recalls and Supply Chain Management"?
Yes, you can pay experts at Fern Fort University to write a custom case study solution that meets all your professional and academic needs.
Do I have to upload case material for the case study Unsafe for Children: Mattel's Toy Recalls and Supply Chain Management to buy a custom case study solution?
We recommend to upload your case study because Harvard HBR case studies are updated regularly. So for custom solutions it helps to refer to the same document. The uploading of specific case materials for Unsafe for Children: Mattel's Toy Recalls and Supply Chain Management ensures that the custom solution is aligned precisely with your needs. This helps our experts to deliver the most accurate, latest, and relevant solution.
What is a Case Research Method? How can it be applied to the Unsafe for Children: Mattel's Toy Recalls and Supply Chain Management case study?
The Case Research Method involves in-depth analysis of a situation, identifying key issues, and proposing strategic solutions. For "Unsafe for Children: Mattel's Toy Recalls and Supply Chain Management" case study, this method would be applied by examining the case’s context, challenges, and opportunities to provide a robust solution that aligns with academic rigor.
"I’m Seeking Help with Case Studies,” How can Fern Fort University help me with my case study assignments?
Fern Fort University offers comprehensive case study solutions, including writing, analysis, and consulting services. Whether you need help with strategy formulation, problem-solving, or academic compliance, their experts are equipped to assist with your assignments.
Achieve academic excellence with Fern Fort University! 🌟 We offer custom essays, term papers, and Harvard HBR business case studies solutions crafted by top-tier experts. Experience tailored solutions, uncompromised quality, and timely delivery. Elevate your academic performance with our trusted and confidential services. Visit Fern Fort University today! #AcademicSuccess #CustomEssays #MBA #CaseStudies
How do you handle tight deadlines for case study solutions?
We are adept at managing tight deadlines by allocating sufficient resources and prioritizing urgent projects. Our team works efficiently without compromising quality, ensuring that even last-minute requests are delivered on time
What if I need revisions or edits after receiving the case study solution?
We offer free revisions to ensure complete client satisfaction. If any adjustments are needed, our team will work closely with you to refine the solution until it meets your expectations.
How do you ensure that the case study solution is plagiarism-free?
All our case study solutions are crafted from scratch and thoroughly checked using advanced plagiarism detection software. We guarantee 100% originality in every solution delivered
How do you handle references and citations in the case study solutions?
We follow strict academic standards for references and citations, ensuring that all sources are properly credited according to the required citation style (APA, MLA, Chicago, etc.).
Top Sellers
- Qihoo case study solution
- Supply Chain Analytics to Manage Blood at VHS Blood Bank case study solution
- Business Intelligence Software at SYSCO case study solution
- Nokia's Supply Chain Management case study solution
- Wills Lifestyle in India case study solution
- Can Blockchain Help Château Lafite Fight Counterfeits? case study solution
- Fair Park Covid-19 Mass Vaccination Site (A) case study solution
- FIJI Water: Carbon Negative? case study solution
- Cisco Systems, Inc.: Collaborating on New Product Introduction case study solution
- Ben & Jerry's Homemade case study solution
- Stock-up vs Stock-out: The Inventory Management Dilemma at a Mobile Clinic
- The New War of the Currents: The Race to Win the Electric Vehicle Market
- Barnes & Noble: Managing the E-Book Revolution
- Boeing 787: The Dreamliner
- Implementing LEAN Operations at Caesars Casinos
- adidas Russia/CIS and the Russian Crisis: Retrench or Double Down (A)
- GitLab and the Future of All-Remote Work (A)
- Levi Strauss & Co.: Driving Adoption of Green Chemistry
- Kitopi: The Brave New World of Cloud Kitchens
Referrences & Bibliography for SWOT Analysis | SWOT Matrix | Strategic Management
1. Andrews, K. R. (1980). The concept of corporate strategy. Harvard Business Review, 61(3), 139-148. 2. Ansoff, H. I. (1957). Strategies for diversification. Harvard Business Review, 35(5), 113-124. 3. Brandenburger, A. M., & Nalebuff, B. J. (1995). The right game: Use game theory to shape strategy. Harvard Business Review, 73(4), 57-71. 4. Christensen, C. M., & Raynor, M. E. (2003). Why hard-nosed executives should care about management theory. Harvard Business Review, 81(9), 66-74. 5. Christensen, C. M., & Raynor, M. E. (2003). The innovator's solution: Creating and sustaining successful growth. Harvard Business Review Press. 6. D'Aveni, R. A. (1994). Hypercompetition: Managing the dynamics of strategic maneuvering. Harvard Business Review Press. 7. Ghemawat, P. (1991). Commitment: The dynamic of strategy. Harvard Business Review, 69(2), 78-91. 8. Ghemawat, P. (2002). Competition and business strategy in historical perspective. Business History Review, 76(1), 37-74. 9. Hamel, G., & Prahalad, C. K. (1990). The core competence of the corporation. Harvard Business Review, 68(3), 79-91. 10. Kaplan, R. S., & Norton, D. P. (1992). The balanced scorecard--measures that drive performance. Harvard Business Review, 70(1), 71-79. 11. Kim, W. C., & Mauborgne, R. (2004). Blue ocean strategy. Harvard Business Review, 82(10), 76-84. 12. Kotter, J. P. (1995). Leading change: Why transformation efforts fail. Harvard Business Review, 73(2), 59-67. 13. Mintzberg, H., Ahlstrand, B., & Lampel, J. (2008). Strategy safari: A guided tour through the wilds of strategic management. Harvard Business Press. 14. Porter, M. E. (1979). How competitive forces shape strategy. Harvard Business Review, 57(2), 137-145. 15. Porter, M. E. (1980). Competitive strategy: Techniques for analyzing industries and competitors. Simon and Schuster. 16. Porter, M. E. (1985). Competitive advantage: Creating and sustaining superior performance. Free Press. 17. Prahalad, C. K., & Hamel, G. (1990). The core competence of the corporation. Harvard Business Review, 68(3), 79-91. 18. Rumelt, R. P. (1979). Evaluation of strategy: Theory and models. Strategic Management Journal, 1(1), 107-126. 19. Rumelt, R. P. (1984). Towards a strategic theory of the firm. Competitive Strategic Management, 556-570. 20. Teece, D. J., Pisano, G., & Shuen, A. (1997). Dynamic capabilities and strategic management. Strategic Management Journal, 18(7), 509-533.
Getting Started
- Template setup
- Basic theme setup
- Navigation bar
- Footer options
- Creating your first post
- Creating docs posts
- Enabling comments
- Google Analytics
Product Features
- Hero page header
- Category boxes section
- Fearured docs section
- Video lightbox boxes section
- Frequently asked questions section
- Team members section
- Call to action section
- Creating a changelog
- Contact form
- Adding media to post and doc content
- Adding table of contents to docs
- Adding alerts to content
- Customization
- Translation
- Development
- Sources and credits
- Contacting support
- Case Studies
- Essays & Term Papers
- Strategy Case Studies
- Marketing Case Studies
- Organization Behavior
- Business Government
- Business Ethics
- Entrepreneurship
- General Management
- Human Resource Management
- Social Enterprises
- Negotiations
- Operations Management
- Information Technology
- Service Management
- International Business
- Miscellaneous
VLU - Week 3 - Mattels Supply Chain
Related documents.

Add this document to collection(s)
You can add this document to your study collection(s)
Add this document to saved
You can add this document to your saved list
Suggest us how to improve StudyLib
(For complaints, use another form )
Input it if you want to receive answer
Pardon Our Interruption
As you were browsing something about your browser made us think you were a bot. There are a few reasons this might happen:
- You've disabled JavaScript in your web browser.
- You're a power user moving through this website with super-human speed.
- You've disabled cookies in your web browser.
- A third-party browser plugin, such as Ghostery or NoScript, is preventing JavaScript from running. Additional information is available in this support article .
To regain access, please make sure that cookies and JavaScript are enabled before reloading the page.

Your All-in-One AI-Powered Toolkit for Academic Success.
+13062052269
Available 24*7 on WhatsApp / Email
- AI Code Checker
- Plagiarism Checker
- Study Documents
- AI Detector
- Terms of Use
- Privacy Policy
© 2024 | Zucol Services PVT LTD | All rights reserved.
Finding Skilled Workers for Supply Chain Management: A Case Study of Mattel Inc
Added on 2023/06/15
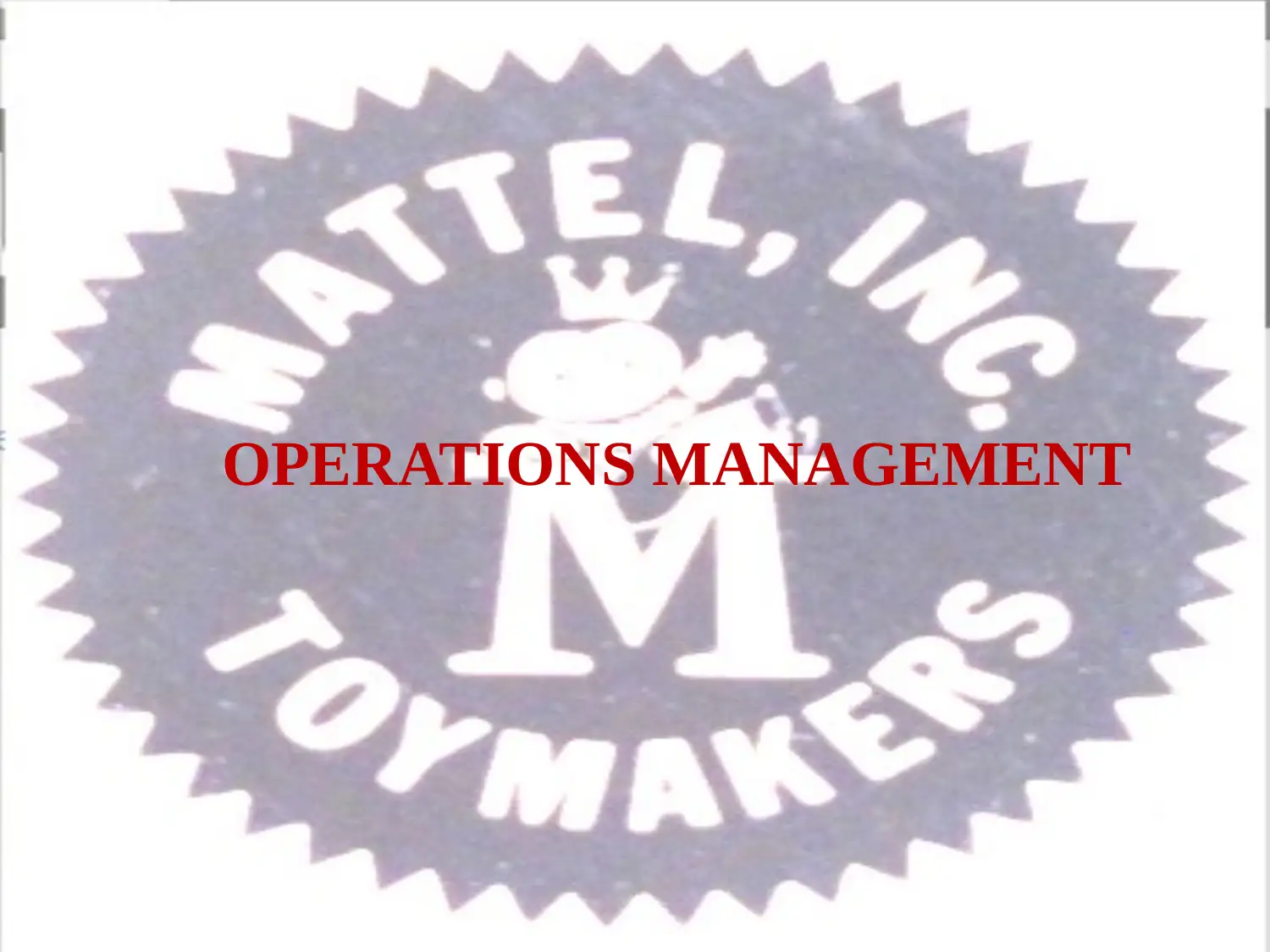
Secure Best Marks with AI Grader
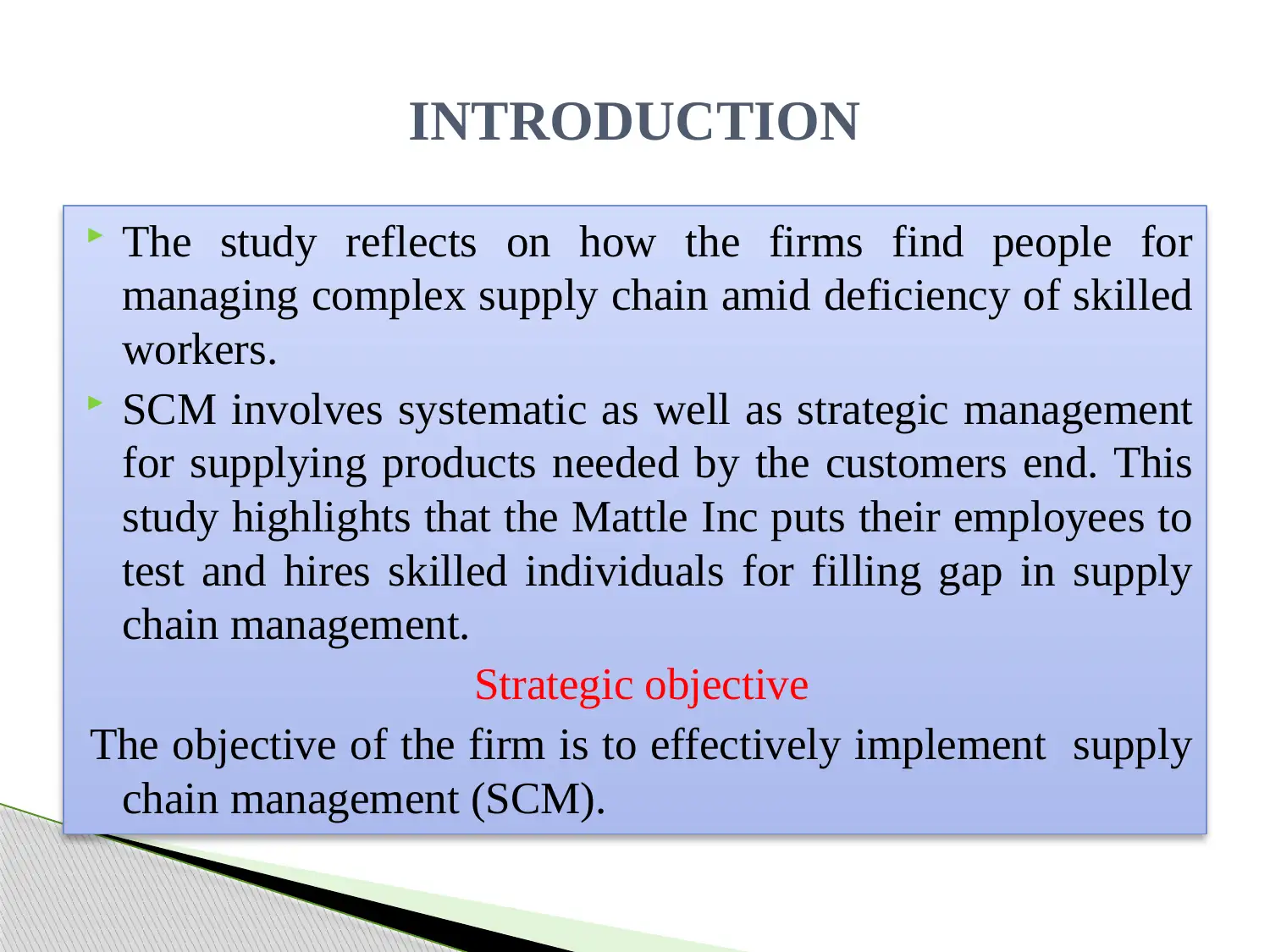
Paraphrase This Document
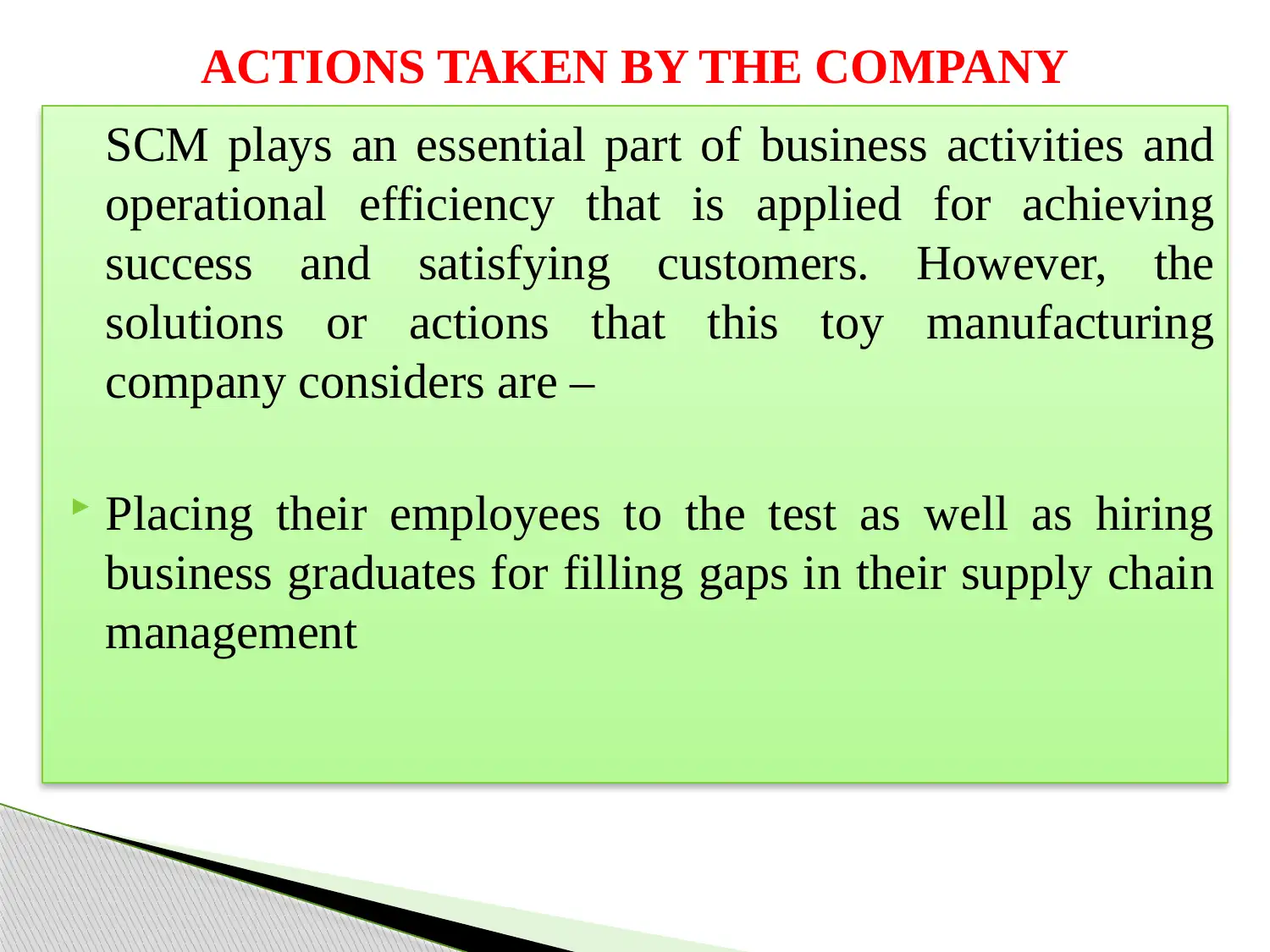
Related Documents

KSAOs for Team-based Job Recruitment

Recruitments and Retention strategies for Desklib

Talent Management: Strategies for Employee Development and Succession Planning

Volkswagen HR Practices Analysis

Importance of HR Strategic Plan for Desklib

Report on Performance of Apple Inc. (Operating in Russia)

Product details

Teaching delivery modes

- For educators
- English (US)
- English (India)
- English (UK)
- Greek Alphabet
This problem has been solved!
You'll get a detailed solution from a subject matter expert that helps you learn core concepts.
Question: Unsafe for Children: Mattel's Toy Recall and Supply Chain Management case study Case Study Questions 1. why do companies outsource? 2. What were the primary causes of Mattel's recall problems? Were these the result of the outsourcing? 3. What actions were taken by the principles in the case to address the recall problems? Were the actions the right
Unsafe for Children: Mattel's Toy Recall and Supply Chain Management case study
Case Study Questions
1. why do companies outsource?
2. What were the primary causes of Mattel's recall problems? Were these the result of the outsourcing?
3. What actions were taken by the principles in the case to address the recall problems? Were the actions the right actions? Why or why not?
4. What Should Mattel do now? What should China do?
5. How can accountability be managed in long, global supply chains?
Introduction:-
Outsourcing has become a common practice in the business world due to various ...

Not the question you’re looking for?
Post any question and get expert help quickly.

IMAGES
VIDEO
COMMENTS
The recalls sparked intense criticism of Mattel and its Chinese supply chain, despite the fact that more than 85 percent of the recalled toys were due to design problems (magnets), not the result of improper manufacturing (use of lead paint). The case provides a basis for discussion of outsourcing and supply chain management.
Uncovering the real nature of the supply chain in the case of exploding pagers in Lebanon will likely remain a mystery. A few entities like Walmart have achieved near total control over their supply chains. But Walmart is the exception. The vast majority of individual firms, including very large firms, do not have the same market power — and ...
Mattel Chief Supply Chain Officer—and CSCMP EDGE keynote speaker—Roberto Isaias discusses how changes to the toy company's supply chain planning process helped it handle the pandemic and the spike in sales from the Barbie ... DCV-TV 1: News DCV-TV 2: Case Studies DCV-TV 3: Webcasts DCV-TV 4: Viewer Contributed DCV-TV 5: Solution Profiles ...
In August and September 2007, Mattel made a series of product recalls, totaling more than 20 million toys. The recalls were for excessive lead and for magnets that could become loose. All of the recalled toys had been made in China. The Mattel recalls followed on the heels of a number of high profile safety problems with Chinese imports, including contaminated pet food and toothpaste ...
On August 14, 2007, the U.S. Consumer Product Safety Commission (CPSC) in cooperation with Mattel announced five different recalls of Mattel's toys. On September 4, Mattel announced three more recalls. Some were due to the use of lead paint, while others were due to small magnets coming loose. The (B) case outlines the handling of the recalls and its consequences, such as consumer outrage ...
However, the large number of actors involved in Mattel's supply chain also revealed an issue of visibility of the supply chain, reducing the possibility to quickly identify non-compliant suppliers. Therefore, the internal structural complexity of the supply chain in this case achieved mixed results.
case of Mattel, Inc. and its toy recalls in 2007 to illustrate handling of the product recall process. 12.1 Introduction So far, we have discussed ways to mitigate various types of supply chain risks rang-ing from supply to demand risks (Chapters 7 and 9), and from financial to outsourc-ing risks (Chapters 8 and 10).
What are areas that require urgent change management efforts in the " Unsafe for Children: Mattel's Toy Recalls and Supply Chain Management " case study. Some of the areas that require urgent changes are - organizing sales force to meet competitive realities, building new organizational structure to enter new markets or explore new ...
This figure translates to over 17,400 kilograms of blueberries lost during transit. There were comparable trends in the trade between Peru and the Netherlands where losses amounted to almost 13.18 percent. These losses emphasize the importance of improving logistics and handling procedures across the supply chain. Potential Pitfalls
The case provides a basis for discussion of outsourcing and supply chain management. The basic toy manufacturing process is fairly simple, providing a forum for discussing these issues without the complication of advanced manufacturing technology or an involved supply chain.
Mattel Tones Down Supply Chain Complexity. For more than half a century, Mattel's Hot Wheels cars have been a toy box staple. Hot Wheels were designed to look like modified hot rods or fantasy cars, often having flames painted on the sides and fantastical proportions. In addition to the toy cars themselves, the accompanying racetrack sets ...
I. Case Study 2 . 1. Overview 2 . 2. Company History 2 . 2.1 Beginnings 2 . 2.2 Reorganization as Mattel, Inc. 3 ... These principles require Mattel's supply chain partners to uphold its stringent standards for safe working conditions, employee health, fair wages, and environmental consciousness. To date, Mattel remains one of the only toy ...
The basic manufacturing process is fairly simple toy, providing a forum to discuss these issues without complications advanced manufacturing or supply chain involved. In this case, supply chain defects, such as the use of lead paint suppliers, can have serious consequences. Supply chain should be designed to prevent these defects.
The recalls sparked intense criticism of Mattel and its Chinese supply chain, despite the fact that more than 85 percent of the recalled toys were due to design problems (magnets), not the result of improper manufacturing (use of lead paint). The case provides a basis for discussion of outsourcing and supply chain management.
Ethical Sourcing, Human Rights and Environmental Standards. We are focused on creating a safe and healthy workplace for all of our employees. We are also proud to support pediatric health services through our work with the UCLA Mattel Children's hospital. Mattel's Responsible Supply Chain Commitment (RSCC) is a comprehensive set of ...
The Unsafe for Children: Mattel's Toy Recalls and Supply Chain Management case study solution undergoes a rigorous quality control process, including multiple rounds of proofreading and editing by experts. We ensure that the content is accurate, well-structured, and free from errors before delivery.
Mattel's supply chain: Case study • Split into groups and discuss the following questions: Based on the case study which supply chain strategy Mattel has adopted? explain and define the meaning of "lean supply" in this context. 1. Explain any benefits and problems for Mattel of adopting this strategy as an approach to managing its supply ...
SCM 110_Supply Chain Administration Case Study #3 and #4 1. How could Mattel have allowed these problems to happen? Aside from simply not using Chinese suppliers, could Mattel have avoided the toy quality/safety problems to begin with? Explain your answers. Answer: By the end of 2007, Mattel had grown rapidly, with worldwide sales of nearly $6.7 billion.
This case study highlights how Mattel Inc overcomes the shortage of skilled workers for managing complex supply chain. Learn about the major issues, actions taken, and recommendations for the company.
For this assignment, read the case study "Unsafe for Children: Mattel's Toy Recalls and Supply Chain Management" on pages 479-491 of your textbook.
Unsafe for Children: Mattel's Toy Recalls and Supply Chain Management. Teaching note. -. Reference no. GS63TN. Subject category: Production and Operations Management. Authors: David W Hoyt (Stanford Graduate School of Business, Stanford University); Hau L Lee (Stanford Graduate School of Business, Stanford University); Mitchell Tseng (Hong Kong ...
After the recall by Mattel, China's export manufacturing sector, an important factor driving country's economic growth, had been stung by suffering highly visible problems. The "made in china" brand was in real danger. At that point. Free Essay: Case Study Mattel's Toy Recall And Supply Chain Management Susita Asree5/11/2014 MGMT 516 ...
Unsafe for Children: Mattel's Toy Recall and Supply Chain Management case study Case Study Questions 1. why do companies outsource? 2. What were the primary causes of Mattel's recall problems? Were these the result of the outsourcing? 3. What actions were taken by the principles in the case to address the recall problems? Were the actions the right